The desire for increased agility in the space environment has prompted research into forms of propulsion that are capable of meeting the objectives of increasingly ambitious missions. While electric propulsion has mostly been used for station-keeping of satellites, its high efficiency has made it a viable and practical option for sending probes to far-off targets.
The Aerospace Corporation is continuing to expand researchers’ understanding of electric propulsion with its EP3 vacuum chamber, a new testing facility for spacecraft thrusters that greatly improves upon the capabilities of its contemporaries, offering testing options on an unrivaled scale.
Spacecraft Propulsion Requires Earth-bound Testing
Electric propulsion involves the application of electricity to ionize gas, which is accelerated out of a thruster to a very high velocity through a combination of electric and magnetic forces.
Unlike chemical propulsion, which provides a high amount of short-lived thrust at the expense of fuel efficiency, electric propulsion offers a low amount of long-lived thrust and high fuel efficiency, making it ideal for long-distance space exploration missions. To make these long journeys, researchers must be certain that spacecraft thrusters can perform consistently and reliably over the duration of a mission.
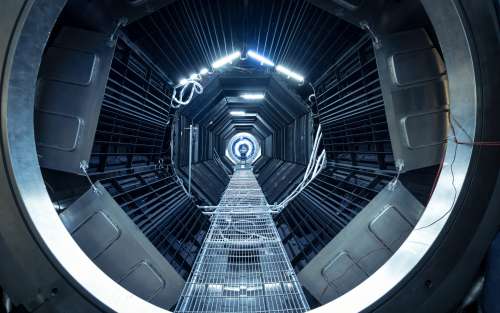
To do so, thrusters must be tested in an environment that replicates space as closely as possible, requiring cryopumps to remove all background gas from the 14-ft diameter by-30-ft long EP3 chamber to recreate the cold vacuum of space.
“As on-board satellite power is increasing, people are developing bigger, more powerful thrusters that have more gas flowing through them, so we needed a chamber that could test the next generation of high power electric propulsion devices. That is why we built EP3, and it's unique in a number of ways,” said Aimee Hubble, Department Director of the Propulsion Science Department. “The pumping system, which is so critical to maintaining that space-like background pressure, is the fastest in the country. That lets us test bigger thrusters. We also have some unique diagnostics that help us stand apart and attract customers from the commercial and civil sectors.”
Groundbreaking Research, State-of-the-Art Facilities
EP3 places Aerospace in the vanguard of propulsion research, making its Electric Propulsion Lab the most advanced facility for the study of electric propulsion thrusters in the world. With its increased capacity and size, and the new antechamber for EMI work, EP3 offers the unprecedented ability to test larger, more capable electric thrusters for use in space, providing critical end-to-end testing of thrust, exhaust velocity and impulse, as well as advanced insight into plume characterization and risk mitigation.
“Unlike its predecessors, EP3 can very, very efficiently channel propellant gas and collect it on arrays, so it's a more open design than has previously been implemented,” said Mark Crofton, Senior Scientist at Aerospace. “With that comes a higher capability, a higher pumping speed and the ability to maintain the vacuum of space in a higher fidelity way. There's also a new generation of devices coming along, so the field is continuously changing. It's growing exponentially and the use of certain types of propellants is no longer set in stone. All sorts of things are on the table, so there's a huge amount of testing and research yet to be done.”
New Capabilities Yield New Insights
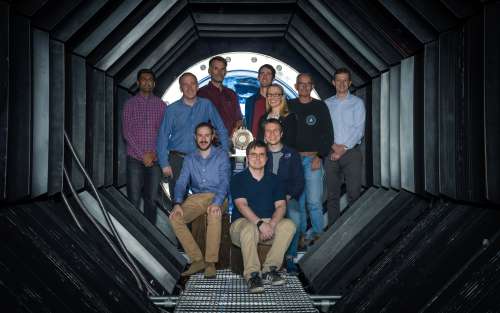
EP3 offers the best predictive capability for in-space electric thruster performance and spacecraft interaction effects, further expanding Aerospace’s mission assurance capabilities. The facility’s augmented potential promises invaluable insight into electric propulsion and its implications for future space exploration, and a growing number of upcoming test activities are currently lined up to provide critical data to a wide variety of customers.
“EP3 has diagnostic capabilities that are unique to Aerospace. We’re the only facility in the country capable of providing them,” said Nicolas Rongione, Member of Technical Staff. “The flexibility of EP3 allows for new diagnostic tools to be integrated as needed. And we’re working with our customers to identify what their needs are and build capabilities to help anticipate future needs.”