Losing weight is never easy—even for space systems. Recent guidance will help analysts predict mass growth and prevent painful mass reduction efforts.
In 2012, the James Webb Space Telescope exceeded its target launch mass by more than 12 percent. An intense, 13-month effort eventually brought the vehicle mass back within allocations, but not before adding almost $1B to the price tag and two years to the schedule.1
Mass growth can be costly, as this example clearly shows. Well-managed programs continuously track vehicle mass status, expenditures, and critical paths. Failure to do so invariably leads to rework, resulting in budget overruns and schedule slips. Rigorous control of mass properties must be maintained during all stages of acquisition, design, manufacture, and test.
Vehicle Mass is Crucial to Acquisition Choices
For example, during the acquisition phase, mass and mass growth are not only primary factors in selecting a suitable launch vehicle but are also among the best indicators of initial cost and sizing requirements. To support this phase, Aerospace developed the Satellite Weight Growth Database, containing mass property details and trends for more than 65 vehicles. This data supports critical decisions, particularly with regard to rapid procurement of space vehicles in a dynamic launch market.
Recently, evolving threats have prompted changes to known space vehicles. Programs are incorporating new hosted payloads, technology insertions, and rad-hard designs, each contributing to mass growth uncertainty. The database enables analysts to forecast weight growth resulting from such changes late in the design phase.
Mission Performance Relies on Proper Vehicle Mass Estimation
Program managers often overlook the wide-ranging impact of mass properties at the subsystem level. Mass properties affect calculations of coupled loads, jitter, motor alignments, stress analyses, and trajectory. They also influence the sizing of structural, propulsion, and control subsystems. Inadequate control of mass properties during development can severely degrade mission performance.
Accurate trajectory insertion demands extremely tight apogee motor alignments. In fact, in some cases, vehicle level center of gravity uncertainties must be as low as 0.02 inches. To achieve such tolerances, it is important to verify and validate all shortages and overages while ensuring ground-support and measurement equipment is properly configured and calibrated.
Accurate mass properties are critical for planning nearly all space maneuvers, including rocket stage separations, satellite deployments, orbital transfers, on-orbit station-keeping, and final deorbiting. Inaccurate data can result in severe mission shortcomings. For example, misalignment of an apogee motor’s thrust vector due to center of mass uncertainties could degrade stability control margins, while excess dry mass could reduce allowable propellant loading, thereby limiting life on orbit.
Vehicle Mass Properties Guidance
Recently published tailoring guidance for the industry standard for mass properties control includes a compliance table to provide applicability cases based on mission risk class.2 Coupled with historical data, the guidance can help analysts forecast growth and risks, determine optimal sizing of vehicle subsystems, and minimize the likelihood of painful and costly mass reduction efforts.
REFERENCE
1James Webb Space Telescope: Actions Needed to Improve Cost Estimate and Oversight of Test and Integration, U.S. Government Accountability Office (Washington, D.C., 2012).
2TR-2018-01203, Tailoring for ANSI/AIAA S-120A-2015, Mass Properties Control for Space Systems: Space Vehicles, The Aerospace Corporation (El Segundo, CA, 2018).
This story appears in the March 2019 issue of Getting It Right, Collaborating for Mission Success.
Subscribe to Getting It Right
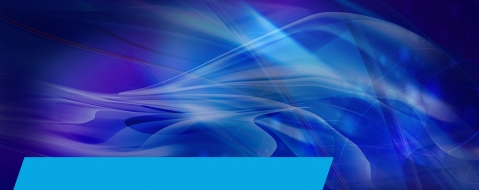